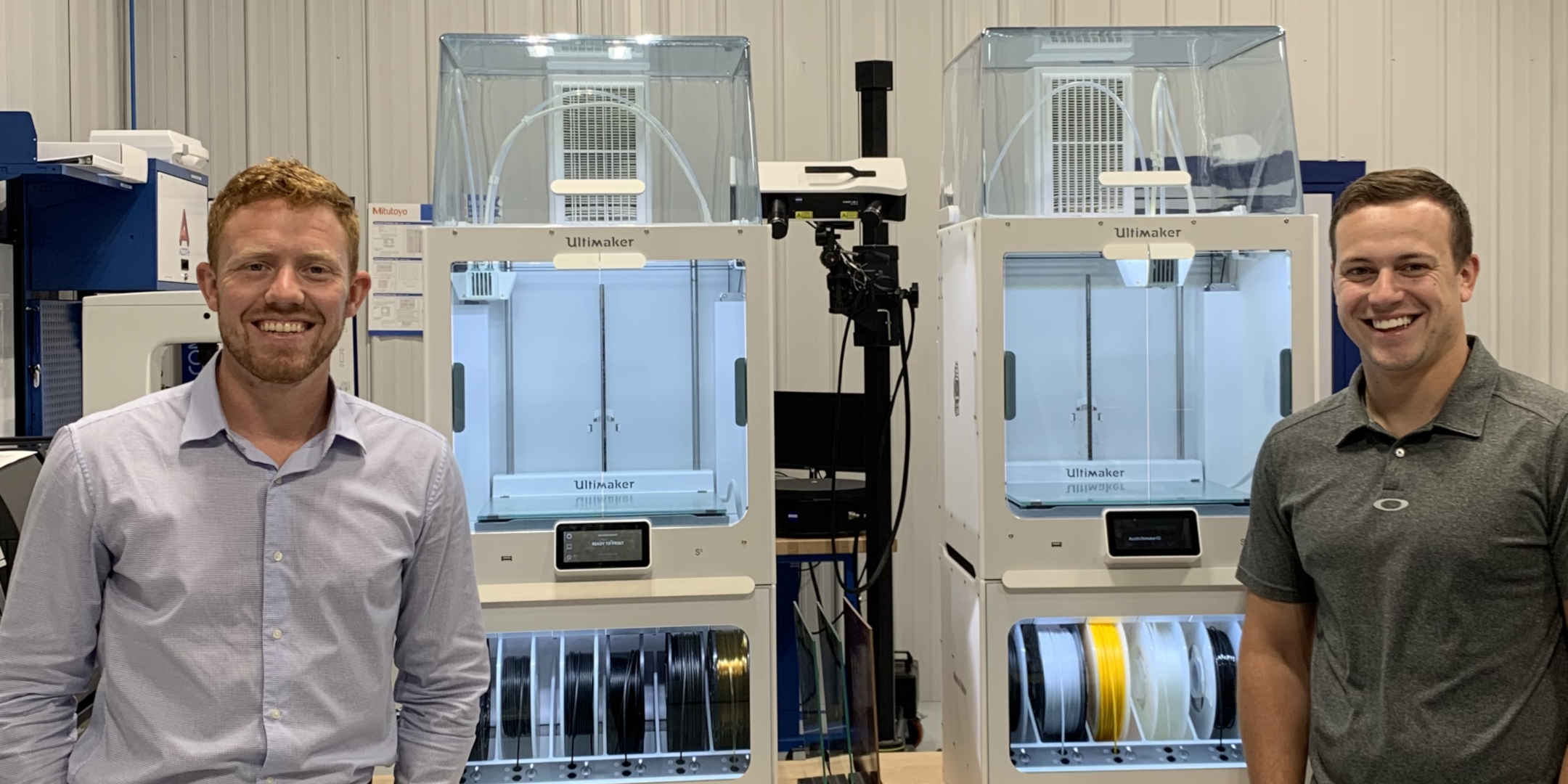
The ‘pro’ in productivity: Cody Cochran talks manufacturing and 3D printing
Cody Cochran is the cofounder of Azoth LLC, an Ann Arbor, Michigan-based organization that focuses on combined traditional manufacturing quality with the efficiencies of rapid prototyping. He is also one of 2020’s Ultimaker Innovators.
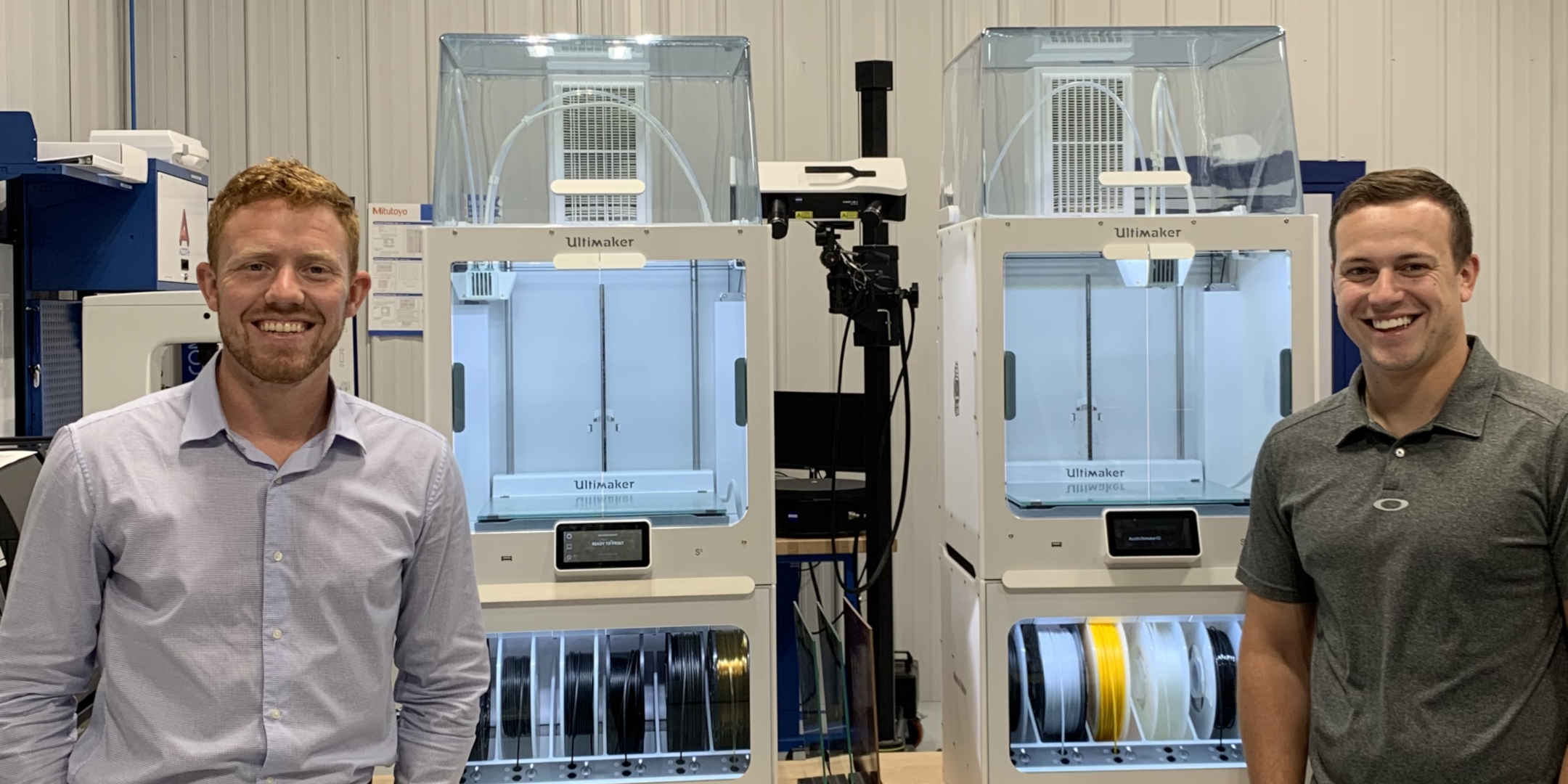
At Azoth, Cody focuses on combining traditional manufacturing quality with the efficiencies of rapid prototyping. As cofounder of the Ann Arbor, Michigan-based organization, Cody Cochran uses Ultimaker 3D printers to help enables its “Take One Make One (TOMO)” digital inventory model inside of manufacturing facilities. The team seeks out parts that will benefit from being produced additively – and with no tooling, tool setup, or minimum order quantities – resulting in time and cost savings.
Here, Cody will touch on several ways that 3D printing is transforming (or has transformed) the manufacturing industry – and, in turn, the ways in which Azoth does business.
Tool and part creation – function over flash
“The average person wouldn’t find these parts – jigs and fixtures, gripper fingers, blow-off nozzles, gage handlers – sexy in any way,” Cody says. “But these are the workhorse parts that enable production to continue. We work to eliminate machine downtime on our customers’ shop floors, reduce complexity, reduce cost, and shrink physical inventory. And we have been successful at it!”
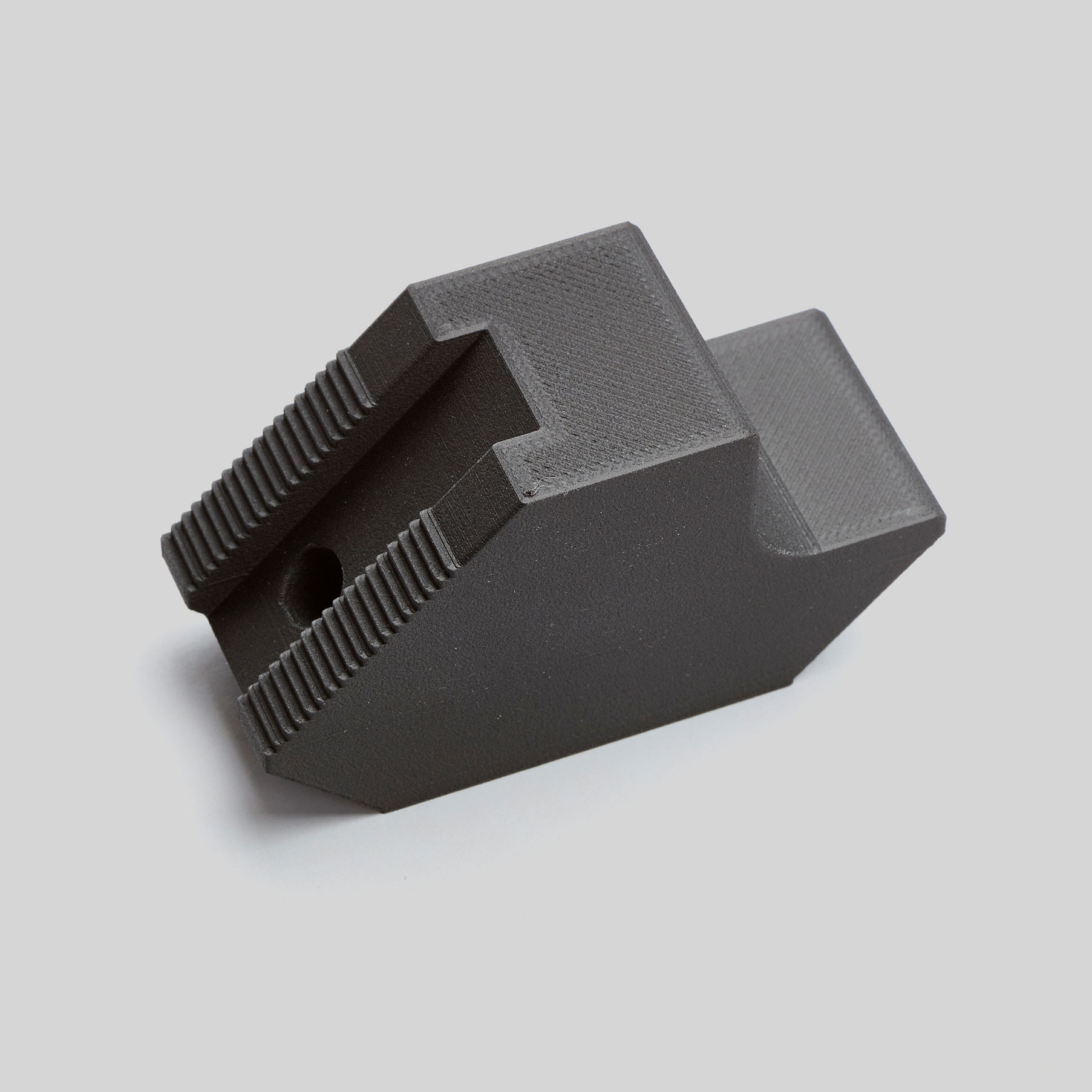
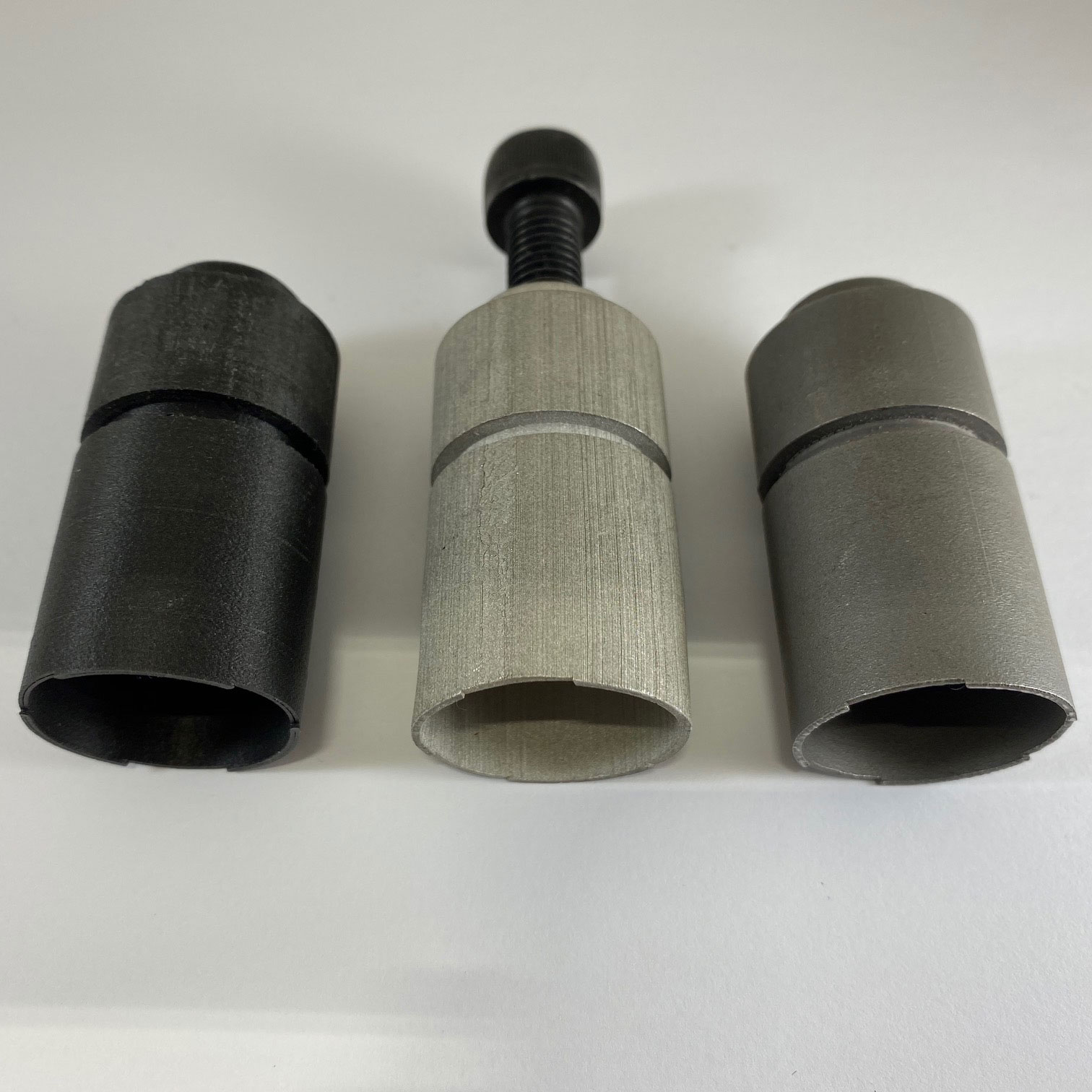
Continuous work is invaluable
“Our Ultimaker S5 Pro Bundle runs six or seven days a week non-stop, creating hundreds of parts each month,” Cody says. “We made them key in our distributed manufacturing workflow and encourage our customers to add on-site Ultimaker 3D printers to their digital inventory strategy. Our Ultimaker S5 Pro Bundle was an immediate cost-saver upon arrival. And it continues to save money, even in the long term.”
Scalability and reliability are customer convincers
"Daily, we are changing mindsets within our customers as we deliver valid business cases on their parts inventory using additive manufacturing,” Cody says. “With Ultimaker 3D printers and materials, the cost is right—they offer easily scalable production and a reliability that we couldn’t have anticipated."
3D printing is a tool, not a replacement
"3D printing won’t replace distributed manufacturing, but it’s a valuable tool that everyone should have in their manufacturing toolbox,” Cody says. “Ultimaker is key in the distributed manufacturing element of our TOMO strategy. Only we use a part on-site, we will print a new one, keeping our inventory light, flexible and deployable wherever we need it.”
Want to learn more about just how Azoth is making waves in the manufacturing industry? Check out its Ultimaker success story, where you get an up-close view of the TOMO strategy – and specific tools and parts – and take a look at pre- and post-3D printing cost and lead times.
You can also download our white paper, “3D printing: The Total Cost of Ownership.” With it, you’ll take a deep dive behind the printer’s price tag to list all the 3D printing workflow costs that you should expect to pay.